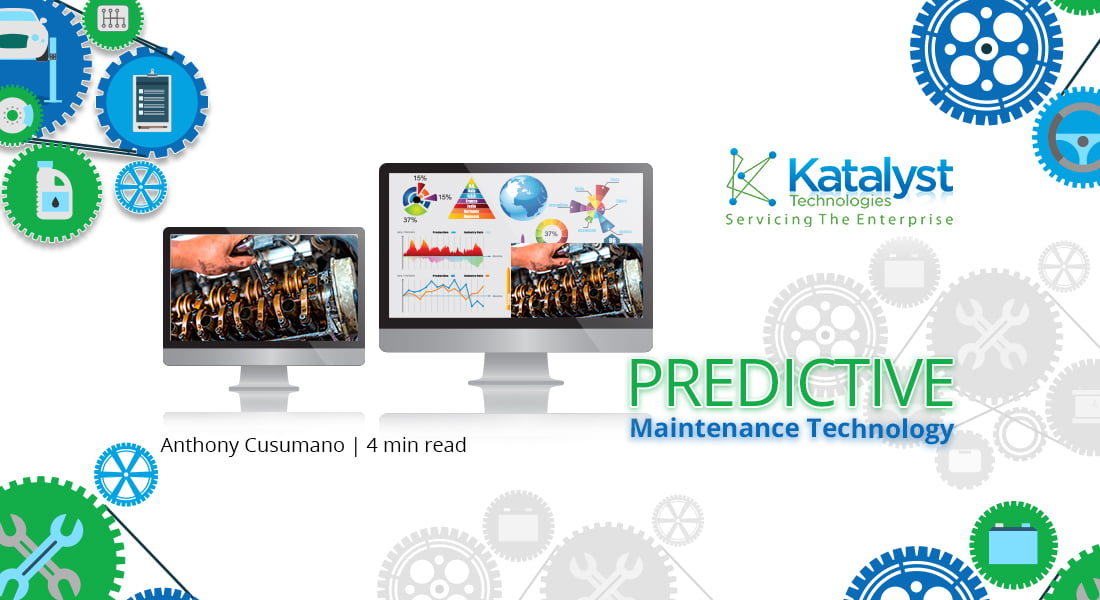
When Lucy Ricardo and Ethel Mertz agreed to a “grass is always greener” role swap with their husbands in a 1952 episode of the seminal I Love Lucy, the pair took on jobs at a chocolate factory. Quickly demoted to the wrapping department, Lucy and Ethel found themselves face to face with a candy conveyer belt. Under the threat of dismissal, “if one piece gets past you and into the packing room unwrapped,” the duo resorted to stuffing chocolates into their mouths and hats when the machine proved too fast for them to keep up. The unknowing foreman returned and, pleased with the perceived progress, instructed the person running the machine, “Speed it up a little!”
No production facility will run efficiently if Lucy and Ethel work there, but regardless of the employees, that machine won’t last forever (and speeding things up will also hasten its need for repair and its eventual demise). Whether you’re operating a chocolate factory, a warehouse, or a manufacturing plant, failing to maintain machinery can lead to decreased productivity, significant expenses, and lost sales. The rise of AI has led to the idea of predictive maintenance, in which computers monitor certain conditions to deduce when a piece of equipment is on its last legs.
Preventative vs. Predictive
Rather than waiting for a breakdown, companies generally take the offensive and adopt a preventative maintenance schedule, relying on past experience and analysis to repair equipment on an ongoing basis. It is a strategy based on consistency, and it’s been ingrained on every level—drivers going in for an oil change every couple thousand miles, for example. The downside, though, is that it can result in unnecessary and premature upkeep. Predictive maintenance eliminates that necessity.
“All forms of maintenance are good because it keeps things running well,” says Steven Hopper, founder of Inviscid Consulting. “The [benefit to] predictive maintenance is that, based on using statistics and algorithms that have come out of research and all of that, these systems and these methodologies end up driving the maintenance process automatically and sort of take the guesswork out of how to maintain it.”
Typically, companies will employ a computerized maintenance management system (CMMS) and sensors to monitor the machines and report on their exact condition. This process provides real-time data about the measurements of factors like temperature, pressure, oil levels, and more. While this information is valuable, it’s worth noting that predictive maintenance might not be the most efficient course of action for every piece of equipment. Use reliability-centered maintenance to develop a variable strategy. The experts at Katalyst can assist with this.
“Positive Harm”
In supply chains, the commonly held belief is that the fewer touches, the fewer mistakes. That’s also one of the key benefits of predictive maintenance. By offering more certainty over the necessity of a given repair, companies avoid the possibility that maintenance might actually do more harm than good.
“Inspection tends to increase breakdowns,” observed British scientist CH Waddington in 1943. “It is doing positive harm by disturbing a reasonably satisfactory state of affairs.” His theory that preventative maintenance actually led to the unplanned failures it was intended to counteract is so lauded it became known as the “Waddington Effect.”
Of course, there are downsides to subscribing to the Waddington Effect. Wayne Gretzky earned motivational poster immortality when he quipped that you miss 100% of the shots you don’t take, and Hopper echoes that sentiment. “If you think about maintenance, you’re going to miss 100% of the problems you don’t look for,” he says. “There could be underlying issues that could turn into bigger problems that, if you’re not doing inspections, you’re unlikely to uncover.”
Is Predictive Maintenance Worth It?
Predictive maintenance is by far the most technology-dependent system of equipment upkeep and requires both the most complex training and most significant initial expense. However, with the right research and proper implementation, it can eventually provide the most substantial ROI.
“Predictive maintenance goes to a whole new level mathematically,” says Hopper. “It’s quantitative instead of qualitative.”