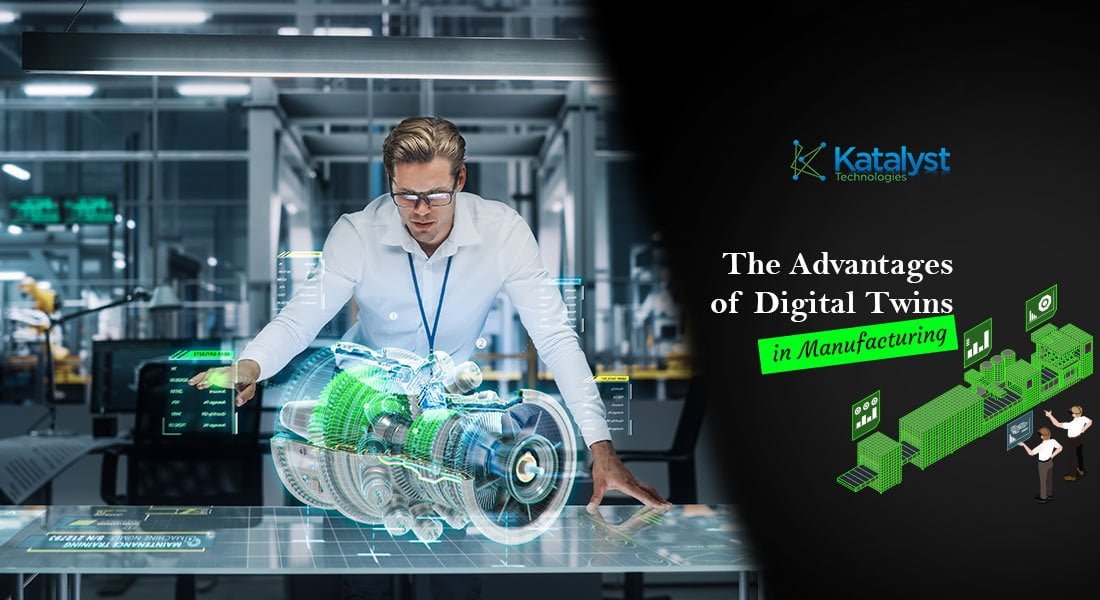
With digital twins in manufacturing technology rapidly advancing thanks to the push towards Industry 4.0, your business can make more products, as well as increase their complexity. The one downside? There is so much more that you need to keep an eye on in your workplace to ensure your supply chain and logistics run smoothly. But what if there was a way you could keep track of your assets without constantly performing in-person inspections?
Through the implementation of digital twins in manufacturing, you can represent products virtually so you can optimize your productions with minimal risk. Once integrated, you will have a far greater insight into your manufacturing process than ever before, as well as what may be to come, cementing them as one of the most important engineering solutions you can invest in.
How do digital twins work?
Much like the other Industry 4.0 technologies we’ve touched on, digital twin technology can be a little hard to comprehend initially. Gaining popularity in the 2010’s, it is easiest to imagine digital twins as the link between your warehouse’s physical and digital worlds.
Through the collection of data throughout your workplace from smart sensors throughout your production line, a digital twin processes this information and applies it to a virtual model. Being an exact version of a process, system, or product of your choosing, this digital setup can replicate your physical one flawlessly, so you can see how it runs in real-time from wherever you may be, differentiating it from a simulation.
In short, think of it as having the best team of technicians, monitors, and engineers at your disposal, checking out all aspects of your operations anytime you need it allowing you to push greater innovation within your business.
Product twin
A Product twin functions as a virtual prototype to foresee its performance, and any issues arising in the production process.
Process twin
These virtual simulations show the manufacturing process, allowing you to test various scenarios to see how well your production line can handle any disruptions.
System twin
Like the title suggests, this particular twin is a virtual model of your entire system. By collecting all your data, you can gain a better understanding of how your entire setup functions.
How can it help you?
Digital twin technology is pretty much essential nowadays if you work in manufacturing for its “big-picture” view of business operations, but if you are just starting out or wish to implement more in your processes, here is how virtual models can benefit you:
Cut costs
Most products go through several rigorous prototyping and testing processes before they hit the production line. This is all perfectly normal and a vital step, but also it can be very expensive and time-consuming.
Digital twins can greatly simplify this process thanks to their ability to fully render products virtually. Instead of spending time and money constantly changing physical prototypes, you can make modifications and run tests instantly, eliminating any risk of issues occurring in the future.
Improve Optimizations
With as many systems your production line is likely juggling, it can be hard to make meaningful changes without possibly throwing the entire setup in jeopardy. A digital twin can recreate a certain process or entire system inside a virtual environment, allowing you to modify various aspects through the data it took in from your physical setup.
Let us say that a particular machine is running slower than usual or is malfunctioning, causing defects in products. Instead of shutting everything down to figure out the issue, a digital twin can replicate the machinery and note that a part is worn out, requiring replacement. It could even notice issues before they even become problems, saving you loads of time in the future.
Reduce time to market
When you are competing with other businesses, it is absolutely crucial to get your product out first to beat them to the punch. But with supply chain disruptions as bad as they are lately, it is getting more difficult to prepare yourself for the market on time.
Building your product, as well as replicating your production line, through a digital twin from the beginning of the design phase can give you the advantage. Not only can you start production sooner, but you can also see how quickly you could make an optimal amount to ship off in time for deadlines.
Katalyst can optimize your business
One of the main goals of Industry 4.0 is ensuring that your operations run as efficiently as possible, but figuring out the best methods to implement technology like AI or digital twins can overwhelm even the most experienced manufacturer. At Katalyst Software Services Limited, our team of trained professionals can offer the best manufacturing engineering services to help guide you through your business’s digital transformation
Feel free to contact us today to learn more about the benefits of digital twins and check out our other posts on the many Industry 4.0 advancements that can assist your manufacturing and engineering business!